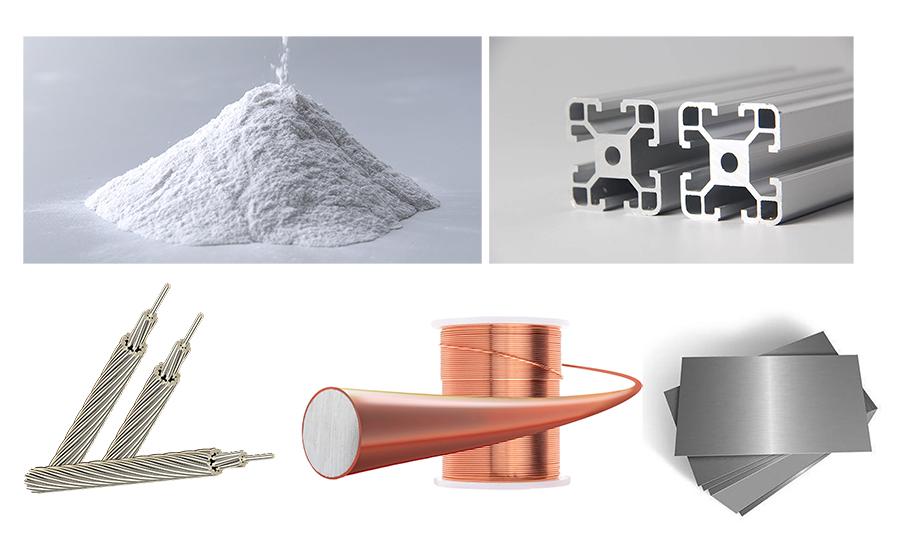
Aluminum is one of the most common elements in the world. It is a good conductor of heat and electricity as well. The main uses for aluminum are in building construction, transportation, and in cooking utensils. Aluminum also has a low melting point which means that it can be melted down easily into liquid form.
Previously aluminum was only present in the form of bauxite. It was mined out of the ground and purified before it could be used for anything except ornaments. Aluminium is a type of metal that has one valance electron and an oxidation level of +3.
Here’s everything you need to know about the different types of aluminum, including a discussion of the features and drawbacks of this metallic element, the various ways it can be used at home, and other helpful tips.
Wrought aluminum
Wrought aluminum is created by applying pressure to molten metal. It turns out at a higher quality than cast aluminum and it is often used for building construction because of its durability.
Sheet aluminum
Sheet aluminum is also another example of a wrought product. The metal is made into sheets and then rolled to make it even thinner before being stamped or cut into the desired shape. This type of aluminum is very light, making it perfect for use on airplanes and large boats. Powder Making Aluminum Alloy
Making wrought aluminum requires a solid bar of aluminum that is heated to an extremely high temperature. The material then goes through a process called extrusion where the molten metal is squeezed into long tubes while at the same time, it’s reduced in thickness and lengthened. This allows many layers of aluminum to be added together to create extremely strong yet lightweight products like bicycle frames.
Clad Aluminum
This type of aluminum is made from two or more layers of 100 percent aluminum alloy. The outer layer can be polished to create an attractive finish and then the core material remains protected from scratching and other types of damage. It is also more durable and stronger than pure aluminum alone.
Extruded aluminum
Extruded aluminum is created on-site by forcing the molten metal through dies which shapes the material into different forms.
Mylar Aluminum
This type of aluminum is created by coating one side of the aluminum with a thin layer of polyethylene, a polymer resin that is also used in plastic bottles. The benefits to this process are high strength and good heat transfer properties. It's often used in things like cooking pots, pans and other kitchen appliances.
Bare Aluminum
Bare aluminum is the pure form of aluminum without any additives. It is often used in coatings since it has a lower resistance when compared to cupo alloys. The end result is that bare aluminum produces heat more easily than other types of alloy but it's also more expensive and not as durable.
It can be used on wires and other electrical applications.
Aluminum Oxide
This type of aluminum is used to create an outer layer on the surface of other types of metal, including copper, iron and lead. It's very easy to weld using techniques like gas welding and it can also be painted after it has been exposed to extreme heat. This makes it perfect for use in things like airplane wings and other structural parts.
Aluminum Nitride
This type of aluminum is used for applications where a high level of thermal conductivity is needed. It's often used in very large industrial equipment since it doesn't lose heat quickly and because it’s so lightweight, makes the machines run faster and more efficiently.
Electrolytic Aluminum
This type of aluminum is created by dissolving scrap metal in an electrolyte solution. Then a positive electrical current is used on one side to produce a highly pure product while the other side can be remelted and reused later.
Aluminum Manufacturing Alloys
There are many types of aluminum alloys that are used for manufacturing parts. The most common is 6061 which is one of the strongest forms and it's resistant to corrosion, quite flexible and can be easily welded. It's also less expensive than other types such as the 7075 alloy. These alloys may contain elements like copper or silicon which make them more malleable or cost-efficient.
Aluminum
Cast aluminum is made by pouring molten aluminum into a mold. This type of metal originally had to be produced by melting down bauxite, but today it can also be obtained through recycling other metals like bronze or steel. Cast aluminum has a low melting point which makes it easy to use for cooking utensils and other simple products.
Most Flexible Aluminum
Alloyed aluminum is an alloy that contains other elements besides aluminum. Alloying allows impurities or additional materials to be added to the metal, making it stronger and more versatile. Some of the most common alloys include bronze, brass, and steel. Alloyed aluminum has a higher melting point than pure aluminum but is still relatively easy to melt down.
Aluminum can be quite flexible. A good example is aluminum foil, you can use it to wrap things up in so many different ways that I lost count. This kind of flexibility is possible because aluminum does not have a very high melting point or boiling point, allowing the metal to easily change shape and form into your desired shape.
Cast Aluminum
This type of aluminum is most commonly known as pot metal or die cast metal. To make this type of alloy, the raw aluminum is cast into a mold and the oxygen in the air burns off. All that remains in the pot are pure aluminum pieces that can be melted down to produce more aluminum sheets, pots, pans and other objects.
Cast aluminum can be made in a few ways. It is either sand cast, permanent mold cast, or die cast. Sand casting is the oldest of the three methods but still widely used because it can produce large objects like automobile engines and parts that are needed for trucks and buses.
Hardest Aluminum Alloy
Die casting is the second most used method of producing cast aluminum. It's done in a machine that applies high pressure to the aluminum and then injects it directly into a mold, hence its name. Die casting creates metal parts with complex shapes for things like automobile interior components, as well as other more complex objects needed by larger machines.
Cast aluminum is hard on the Mohs scale at a 5. This means that it won't scratch easily and can be used to create objects that are resistant to scratches. Cast parts are also very cheap when compared to other types of metal, making them a good alternative for parts that will get greasy or dirty.
Household products using aluminum
Aluminum Siding
Aluminum siding is used to make siding for homes and businesses because it’s durable, has great strength and can be easily painted to hide any imperfections. It's often put on in sheets or panels that are backed by foam insulation or other types of plastic materials. Aluminum siding is also being replaced with fiberglass which is not as strong or durable but it's also cost-efficient to produce.
Aluminum Roofing
This is used in roofing to provide durability and shed heat. It can also be painted over any defects although the material does deteriorate over time due to natural elements like wind, rain and sunlight.
Aluminum Furniture
Aluminum is very sturdy and durable so it is used in the production of furniture. It can also be easily painted or powder coated to hide scratches and other types of surface damage. There are many different types of aluminum furniture such as chairs, shelves, beds and tables which are becoming more popular because they're much lighter than wood yet just as strong.
Exterior Buildings
Aluminum is often used in the exterior coating of buildings for decoration and protection. It can also be used on window frames, doors and other parts of a building.
Aluminum Foil
Aluminum foil is made from thin sheets of aluminum that are coated with either a plastic or paper layer. It's often used to wrap up food and then thrown away since it can be easily recycled. Aluminum foil is also being replaced by the “microwave safe” plastic materials now because they're cheaper and more versatile.
Aluminum Pots & Pans
Aluminum is a great conductor of heat and it's used to make pots, pans and baking sheets because they’re strong enough to handle the weight while being very lightweight.
Aluminum cans
There are many different types of aluminum alloys. The most common is pure aluminum, also known as 100 percent aluminum alloy. This type of metal is preferred for applications where a large amount of heat needs to be transferred to liquid inside the container like in beverage and food containers. Pure aluminum is very soft and can scratch easily but it is also very light and inexpensive.
Cupo Aluminum
This is a type of aluminum alloy that has an electrical resistance that is lower than 100 percent aluminum. It has better resistance to corrosion and because it's cheaper, it's sometimes used in places where the high cost of other types of metal would be difficult to justify. This product is also used in things like automotive parts, wires and cladding on building surfaces.
FAQS:
What are the most common types of aluminum alloy?
Aluminum is created by dissolving scrap metal in an electrolyte solution. Then a positive electrical current is used on one side to produce a highly pure product while the other side can be remelted and reused later.
The most common type of aluminum alloys are 6061 which is one of the strongest forms and it's resistant to corrosion, quite flexible and can be easily welded. It's also less expensive than other types of aluminum like the 7075 alloy which contains elements like copper or silicon which make them more malleable or cost-efficient.
What are the advantages of using aluminum over other types of metal?
It's one of the most common lightweight metals that can be easily molded so it's often used for things that need to be fastened together or mounted in a fixed position. It also doesn't rust and is often paired with plastic to make it more durable.
What are some of the disadvantages of aluminum?
Because aluminum isn't very strong on its own, many times it's combined with other metals to create something that's more cost-effective and sturdy. The main disadvantage is that it can be easily scratched, especially if you're not careful when you're working with wood or other materials.
What are some uses of aluminum in the medical field?
It's often used in medical devices such as wheelchairs and walkers because they’re lightweight but still sturdy enough to provide support. It's also used in syringes and intravenous bags because it’s easy to use and cheap.
What are some uses of aluminum as a coating?
It's commonly used to coat the inside of cans, bottles or other containers that should be lightweight but still strong enough to hold large amounts of liquid for food or beverages. It's also used to coat the inside of pans so food doesn't stick.
What are some uses of aluminum in aerospace technology?
One use is tubes and other parts that need to withstand a lot of heat or pressure without being damaged. It’s also used for its weight, since it's the lightest metal among them all. It can be easily molded into whatever shape is needed so it's often used in building parts that need to be tightly secured.
What commercial uses does aluminum have?
It's a very common metal used for building materials, specifically siding and roofing because it’s inexpensive and durable. It can also be found in items like cookware, machinery or cars.
Conclusion:
There are so many different types of aluminum and it is used in so many different ways that a thorough list couldn’t even be put together. Although it doesn't have the tenacity or thickness of other metal like steel, if treated properly aluminum can provide strength, functionality and appearance for years to come.
The list of uses is infinite because it's one of the most commonly used metals on earth. Aluminum has more than 1,000 commercial applications and hundreds of household applications so it's easily available to be used in a variety of ways.